Injection Molding vs. 3D Printing: Which One’s Right for You?
- MP Webmaster
- Jul 3
- 6 min read
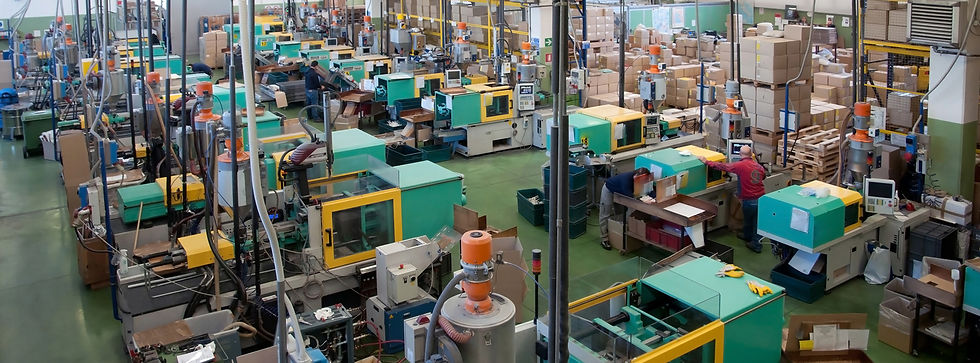
A few months ago, a product design team from a medical startup came to us with a wearable sensor about the size of a quarter. They’d been 3D printing prototypes in-house, testing different layouts and enclosures. Everything looked good on paper. They had interest from investors, a few pilot customers, and real market momentum.
Then came the real question:
“Can you help us make 25,000 of these parts??”
That’s when the conversation moved from “Is it possible to 3D print this?” to “How do we manufacture it—reliably, affordably, and at scale?”
At Moraine Plastics, we’ve seen this discussion unfold more times than we can count. Product teams reach the tipping point where what worked in early development just isn’t going to cut it in full-scale production. And more often than not, the answer isn’t about choosing between 3D printing and injection molding—it’s about knowing when to use each.
Key Takeaways
Injection molding and 3D printing are both popular manufacturing processes with unique advantages and applications.
Injection molding is generally more cost-effective for large production runs, while 3D printing is more economical for small-scale production and prototyping.
Injection molding is faster and more efficient for mass production, while 3D printing offers quicker turnaround times for small batches and custom designs.
Injection molding provides a wider range of material options, including various plastics, metals, and composites, while 3D printing is limited to specific materials such as plastics, resins, and metals.
3D printing allows for more design flexibility and the creation of complex geometries, while injection molding is better suited for simpler, uniform shapes.
Why the Choice Matters
There’s a lot of noise out there—especially around 3D printing. It’s fast, it’s flexible, it’s futuristic. And it is all of those things.
But when someone asks, “Which is better: 3D printing or injection molding?”—they are asking the wrong question.
The better question is:
What are you trying to make, how many do you need, and what do you expect it to do?
Because once you know that, the right process usually reveals itself.
When 3D Printing Works Best
Let’s give credit where it’s due. 3D printing is a remarkable tool—especially in the early stages of product development. It lets you move fast, fail safely, and change your mind without writing a $15,000 check for tooling.
Need a single housing to check fit? Want to try three versions of a snap feature? Curious if your weirdly organic vent pattern will hold up? Print it. See it. Touch it. Break it. Change it. Print it again.
We love how 3D printing lets engineers take risks. It keeps teams from getting locked into decisions too early.
And beyond prototyping, there are a few legitimate cases where 3D printing holds its own in production:
Low-volume or custom parts
If you only need 10 units, and each one is a little different—say, surgical jigs or personalized ergonomic components—3D printing makes perfect sense.
Designs with extreme geometry
Hollow channels, lattices, parts with internal movement? Additive manufacturing can make shapes that are a nightmare to mold.
Fast-turnaround needs
Got a tradeshow in four days and forgot to make demo units? A decent 3D printer can save the day.
But—and this is a big but—3D printing has limits.
Where Injection Molding Takes Over
At some point, every serious product crosses into injection molding territory. Usually when volume increases, tolerances tighten, or the part needs to survive in the real world—not just in a conference room demo.
Here’s where injection molding pulls ahead:
Scale, Efficiency, and Repeatability
Once your tooling is in place, injection molding is a beast. You can make thousands of identical parts with near-zero variation, in a matter of days. That’s why companies choose it for everything from automotive clips to consumer electronics. Speed, consistency, and low cost per part.
“The mold pays for itself over time,” says Gerry Ford, owner of Moraine Plastics. “Our customers aren’t just buying a part—they’re buying reliability. They want to hit a button and know the next 20,000 pieces are going to be dead-on.”
Tougher Materials, Better Performance
Let’s be real—most 3D printing materials aren’t built to last. They’re fine for prototypes and light use, but injection molding opens the door to true engineering thermoplastics.
Want a part that resists UV? Holds up in high heat? Snaps without cracking? Injection molding gives you that. Plus, you can do overmolding, insert molding, and multi-shot molding—all in one cycle.
Moraine Plastics works with a wide range of high-performance materials including ABS, PC, PA, and TPE blends. We help our customers select the right one based on function, finish, and regulatory compliance.
Consistency Under Pressure
3D-printed parts vary—sometimes a little, sometimes a lot. That’s a problem when you’re designing assemblies that rely on tight fits or press points.
Injection molding? No surprises. The tool defines the part, and once it’s dialed in, you’ll get the same result every time.
And if you're working in a regulated industry (medical, food, automotive), you need that consistency—not just for functionality, but for documentation and certification.
Tooling: The Big Hurdle—and the Big Win
Let’s talk about the elephant in the room: the mold.
Tooling is the reason some teams hesitate to move into injection molding. It takes time, it’s an investment, and once the steel is cut, changes aren’t free. That’s fair.
But it’s also where the magic happens.
At Moraine Plastics, we don’t just “take your files and make parts.” We work with you to optimize your design before the tool is built. That means fewer delays, faster cycles, and lower long-term cost. Our tooling partners build high-quality molds that are designed to last—because we know what 200,000 shots looks like.
If you’re in this for the long haul, tooling isn’t a hurdle—it’s an asset.
* Learn more about tooling and part design
Side-by-Side: 3D Printing vs. Injection Molding
Feature | 3D Printing | Injection Molding |
Best Use | Prototyping, low-volume, complex geometry | High-volume production, repeatability |
Tooling | None required | Custom mold required |
Per-Part Cost | High | Very low at scale |
Lead Time | Fast (days) | Longer upfront, faster afterward |
Material Selection | Limited | Extensive, including engineering-grade plastics |
Tolerance/Finish | Variable | High precision, excellent finish |
Speed at Scale | Slow | Extremely fast |
Sustainability | Can be wasteful | Efficient with optimized cycle times |
The Hybrid Approach: Print, Then Mold
In most cases, the smartest path isn’t picking one or the other. It’s using both.
Start with 3D printing to nail down your design, test form and function, and explore options without risk. Then, when you're confident in the final version, transition into injection molding for production.
We do this all the time with our clients. Some even send us their printed prototypes so we can reverse-engineer the mold. It’s a seamless bridge from idea to production—and it works.
The Final Word from Moraine Plastics
There’s no magic formula for choosing between 3D printing and injection molding. But there is a clear decision path when you know your priorities.
If you need speed and flexibility, print it.
If you need volume, precision, and performance, mold it.
If you’re unsure? Talk to a manufacturer who has worked with both.
“The best projects we see,” says Gerry Ford, “are the ones where teams start smart and scale strategically. 3D printing is a great sandbox. But if you want to go to market with confidence, you’ll need to mold it. That’s where we come in.”
Ready to Make Something Real?
If you’re wondering how to take your part from prototype to production—or if you’re trying to decide whether molding is worth it—contact Moraine Plastics. We’ll walk you through the tradeoffs, help you avoid the common pitfalls, and build a process that actually works for your product.
Because for us, it’s not just about making parts—it’s about making smart manufacturing decisions with people we trust.
FAQs (Frequently Asked Questions)
What is injection molding?
Injection molding is a manufacturing process for producing parts by injecting material into a mold. It is commonly used for mass production of plastic parts.
What is 3D printing?
3D printing, also known as additive manufacturing, is a process of creating three-dimensional objects by adding material layer by layer based on a digital model.
What are the advantages of injection molding?
Injection molding is capable of producing high volumes of parts with high precision and repeatability. It is also cost-effective for large production runs and can use a wide range of materials.
What are the advantages of 3D printing?
3D printing allows for rapid prototyping and customization, as well as the creation of complex geometries that are difficult to achieve with traditional manufacturing methods. It also has lower setup costs and is more flexible for small production runs.
Which is better for mass production, injection molding or 3D printing?
Injection molding is generally better suited for mass production due to its high production speed and lower cost per part. 3D printing is more suitable for prototyping and small production runs.
Which process is more cost-effective, injection molding or 3D printing?
For large production runs, injection molding is typically more cost-effective due to its high production speed and lower cost per part. However, for small production runs and rapid prototyping, 3D printing can be more cost-effective due to lower setup costs and flexibility.
Which process is more suitable for creating complex geometries?
3D printing is more suitable for creating complex geometries due to its layer-by-layer additive manufacturing process, which allows for the creation of intricate and customized designs that are difficult to achieve with injection molding.
Which process is more environmentally friendly, injection molding or 3D printing?
Both injection molding and 3D printing have environmental impacts, but 3D printing generally produces less waste material and can be more energy-efficient for small production runs. However, injection molding can be more efficient for large production runs, leading to lower overall environmental impact.